Como o papel é feito passo a passo
O papel é uma folha fina produzida a partir de polpa de celulose proveniente de fibras de árvores. Sua fabricação exige um processo longo e complexo que envolve também um gasto importante de energia e água, com a consequente emissão de gases para a atmosfera, razão pela qual o uso racional do papel é muito importante.
Existem muitos tipos de papel, dependendo do seu uso; de papel higiênico e jornal, a papel kraft, liner, pergaminho, papelão, revestido, autocopiativo, adesivo, metálico, térmico, rótulos, etc.
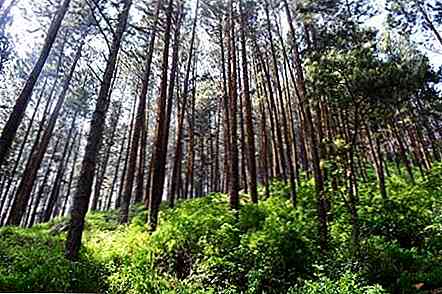
Todos os tipos de papel iniciam a partir do mesmo processo inicial e só variam em sua fase final, onde diferentes componentes são adicionados, dependendo do uso que será dado.
O seguinte explica como o papel é feito passo a passo.
O processo de fabricação de papel
1- Plantação
Este processo começa com o plantio das florestas de árvores para tal destino. São plantações de espécies de crescimento rápido que seguem critérios de sustentabilidade.
2- Descascamento
Quando as árvores atingem a altura necessária, elas são derrubadas e uma vez derrubadas, as árvores são descascadas.
Em alguns casos, como o eucalipto, por exemplo, esse processo é feito manualmente, enquanto no caso de pinus e outras espécies o processo é químico ou mecânico, sendo este último o mais comum.
Essa operação é realizada esfregando-se dentro de um tambor em um ambiente úmido.
3- Armazenamento
A madeira cortada e descascada deve ser armazenada por um longo período para evitar o contágio e evitar o ataque de microrganismos.
No caso das espécies de madeira dura, elas são armazenadas por 6 meses antes de serem usadas; as espécies resinosas, mais de um ano.
4- Esmagamento
Depois de descascar, os troncos são esmagados e reduzidos a pequenos chips conhecidos como chips.
Para atingir um tamanho uniforme, os chips passam por uma série de lâminas e peneiras que rejeitam as peças muito grandes para levá-las de volta ao corte.
5- polpa
A pasta é obtida por tratamento químico da madeira, por meio de fases de cozimento com refrigerante e outros componentes.
6- Branqueamento
A polpa é submetida a um tratamento com peróxido de hidrogênio e oxigênio, embora existam procedimentos mais modernos.
Nesta fase, a madeira é liberada de todos os seus componentes não celulósicos, como a lignina.
7- folhas de massa
Uma vez que a polpa é branqueada, se a fábrica é integrada, ela é enviada através de tubos para a seção correspondente.
Se não for integrado, serão fabricadas chapas de celulose com umidade de 10% para transportá-las em caminhões para outras fábricas de papel.
8- Preparação de celulose
As folhas de pasta de celulose que chegam à fábrica devem ser desfeitas por meio de uma operação realizada no Pulper, que é um recipiente com uma hélice em sua parte inferior que agita as folhas e a fricção faz com que as fibras se soltem.
9- Refinar
Como o Pulper vai mexendo, a pasta passa por uma espécie de peneira que impede a passagem de peças grandes.
Através do refino, a pasta adquire as habilidades específicas que necessita dependendo do tipo de papel a ser fabricado, mas basicamente consiste em passar a pasta através de dois elementos (um fixo e um rotativo).
10- Misto
Após o refino, a pasta é transferida para a cuba de mistura onde diferentes componentes são adicionados, como alvejante (dióxido de cloro, ozônio, enzimas, etc.), agentes de acabamento e preenchimentos que fornecem maior opacidade e melhor qualidade de impressão ao papel.
11- banheira de nível constante
Esta mistura de componentes é enviada para uma cuba de nível constante, onde a massa sempre mantém o mesmo fluxo para garantir uma massa uniforme.
A partir deste momento, a fabricação real de papel começa.
12 - Caixa de entrada
O fluxo de pasta diluída passa pela caixa de entrada e se transforma em uma folha de líquido fina, larga e uniforme, contendo todos os componentes do papel da maneira mais perfeita possível.
13- mesa de fabricação
A suspensão fibrosa é enviada para a mesa de fabricação em um tecido sem fim onde a folha de papel será formada.
Este tecido se move em duas direções: longitudinalmente (também chamado de fibra) e transversalmente (conhecido como contrafibra).
Neste movimento, as fibras do papel são organizadas e isso influencia tanto a qualidade de impressão como a dobragem e encadernação.
14- Orvalho
Quando a pasta diluída atinge o tecido, tem 99% de água e tem que passar por diferentes processos para eliminar seu excesso.
No início, o processo de drenagem é rápido devido à grande diluição da pasta e ao efeito da gravidade, mas depois forma-se uma camada compacta que dificulta a eliminação da água.
Naquele momento, é usada a ação de folhas, caixas de sucção e rolos de drenagem, que agem energeticamente de acordo com a dificuldade de extrair água da folha.
Quando a folha chega ao final do tecido, tem uma umidade de aproximadamente 80% e está preparada para receber mais tratamentos energéticos projetados para eliminar a água restante.
15- Pressionando
A prensa é a seção colocada imediatamente após o tecido e onde continua por meios mecânicos a eliminação de água do papel, passando de 80% para 60%. Na prensagem, até certo ponto, a consolidação da folha é realizada.
16- Secagem
Nesta fase, o excesso de umidade do papel só pode ser removido com o calor. A secagem é geralmente dividida em duas seções nas quais o calor é aplicado ao papel através de grandes cilindros quentes.
O papel puxa-se, o que gera tensões entre as fibras chamadas de tensões internas.
Isso condiciona especialmente a qualidade do papel, uma vez que essas tensões podem causar instabilidade dimensional na impressão.
Máquinas como "Size Press" ou "Gate-Roll" ajudam a resolver este problema aplicando uma pequena camada de aglutinante na superfície do papel para melhorar a resistência ao rasgo.
17- Rolando
Depois de seco, o papel é enrolado em uma máquina chamada "Pope". A partir daqui, o papel pode seguir dois caminhos: se não for revestido, vai diretamente para a seção Acabamentos; Se for revestido, passará pela máquina de revestimento.
18- Estucado
É a aplicação de um tipo de tinta chamada "Salsa" que melhora as condições de impressão do papel.
Este molho é feito na cozinha da fábrica e é composto por pigmentos, branqueadores ópticos, resinas, microbicidas e outros componentes.
Aplica-se por meio de um rolo e dosado e equalizado graças a uma chapa de aço. Seca com raios infravermelhos que aplicam calor no papel.
19- Acabamentos
Quando o papel sai da máquina de estuque, parece mate. Para transformá-lo em brilhante ou semi-mate, é necessário passar pela calandra, uma série de rolos metálicos duros e macios que pressionam o papel e dão origem ao brilho.
20- enrolamento
Finalmente, o papel vai para o bobinador para converter a bobina jumbo em bobinas menores que podem ser enviadas para o cliente ou que seguem outros caminhos a serem transformados em folhas ou outros produtos de papel.
21- Corte
O cortador é a máquina que transforma o rolo de papel em folhas. Possui lâminas muito afiadas para garantir um corte preciso e sem poeira que pode causar problemas de impressão.
22- Embalagem e distribuição
O papel cortado está pronto para ser embalado e distribuído para as saídas finais.
Como pode ser visto, é um longo caminho que começa com uma árvore e termina no papel em que escrevemos, lemos ou empacotamos.
Referências
- Fabricação de papel Recuperado de camarapapel.org.ar
- Conhecer o fabrico de papel, uma vez que é uma árvore. Recuperado de veoverde.com
- Como o papel é feito Retirado de laprestampa.wordpress.com
- Como o papel é feito? Recuperado de creativosonline.org
- Como a polpa de papel é feita Recuperado de ecoempaqes.com.pe
- O fabrico de papel. Recuperado de graciaspapel.es